COPING WITH HARSH HEALTHCARE CHEMICALS
Aggressive healthcare disinfectants can degrade plastics used in equipment housings and device components. Frequent exposure to products like Sani-Cloth AF3 wipes can cause environmental stress cracking, potentially resulting in malfunctions that may interfere with patient care or lead to costly premature failure and warranty claims.
SABIC’s ULTEM™ HU resin series and LNP ELCRES™ CRX copolymer resins deliver exceptional chemical resistance. By helping prevent or mitigate ESC, they can improve device durability, extend useful life and reduce waste for a more-sustainable footprint.
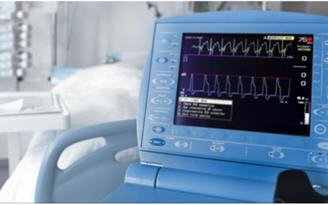
SAILING THROUGH STERILIZATION
Like disinfectants, sterilization can degrade the performance, appearance and integrity of parts. Adding to the challenge are anticipated EPA regulations restricting EtO sterilization emissions. To meet customer needs, the thermoplastics used in your devices should be compatible with multiple sterilization methods and withstand repeated cycles.
ULTEM HU resins, NORYL™ HNA resins and LNP copolymers provide stable performance under repeated cycles of vapor hydrogen peroxide sterilization (ie STERRAD® ), steam autoclave, gamma/E-beam radiation, as well as Et0. Excellent retention of mechanical, thermal and aesthetic properties helps to extend the useful life of medical devices.
PRECLUDING PTFE FOR WEAR AND FRICTION
Proposed regulations severely restricting or banning per- and polyfluoroalkyl substances (PFAS) are prompting device makers to seek lubrication alternatives to PTFE. SABIC’s internally lubricated LNP™ LUBRILOY™ compounds, featuring a patented olefinic additive, offer an alternative to PTFE-lubricated materials. Their excellent wear and friction performance can enhance device reliability and usability and extend service life.
LNP LUBRILOY compounds are available in a wide range of base resins, including PC, PC/ABS, POM, PBT and PEI.
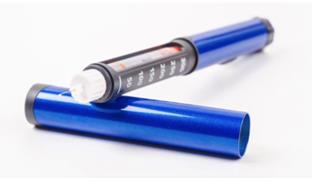
STRENGTHENING STRUCTURAL PARTS
Strength, stiffness and stability are vital for medical and surgical devices subject to applied force, such as skin staplers, retractors, forceps and injection pens. But traditional stainless steel adds significant weight and can hamper design freedom.
SABIC’s ULTEM resins and reinforced LNP™ THERMOCOMP™ compounds can replace metal in structural parts, delivering comparable strength while reducing weight and processing costs and enabling complex designs. These materials help structural components remain strong and precise and last longer to reduce waste.
CONNECTING TO CARE
Wireless connectivity is a critical feature of devices used for remote and mobile patient monitoring, diagnosis and treatment. To help achieve positive patient outcomes, connected devices require specialized materials for accurate, safe, reliable and user-friendly operation.
SABIC solutions for wireless devices include ULTEM resins with good dielectric properties, LNP™ FARADEX™ compounds with EMI shielding capabilities, and transparent, scratch-resistant LNP™ ELCRES™ DMX copolymers for displays. SABIC technologies support advanced manufacturing methods like laser direct structuring (LDS). They even help solve aesthetic challenges of laser welding white and light-colored materials.
SUPPORTING SUSTAINABILITY
SABIC’s solutions can help you increase sustainability by optimizing designs to reduce weight and dimensions and increasing device lifespan with strong, chemically resistant materials that help avoid premature replacement and reduce landfilling.
Innovations such as LNP™ ELCRIN™ iQ resins, made from chemically upcycled PET water bottles, and certified renewable bio-circular versions of ULTEM and NORYL resins, can help reduce carbon emissions without compromising on performance
To discover how SABIC can help you to select the correct material for your medical device, please contact SABIC’s local Irish distributor, Ultrapolymers using ask.healthcare@ultrapolymers.com or visit the website www.ultrapolymers.com.